تجهیزات ابزار دقیق
تجهیزات ابزاردقیق شامل دستگاهها و ابزارهایی است که برای اندازهگیری و کنترل دقیق و صحیح پارامترهای فیزیکی و شیمیایی در صنایع مختلف استفاده میشود. این تجهیزات شامل انواع سنسورها، ترانسمیترها، کنترلرها و نمایشگرهای دیجیتالی میشود که در ادوات دقیق، ابزار دقیق و تجهیزات اندازهگیری کاربرد دارد.
استفاده از تجهیزات ابزار دقیق در بسیاری از صنایع مانند صنعت نفت و گاز، صنایع شیمیایی، صنایع خودروسازی، صنایع الکترونیک، صنایع فضایی و هواپیمایی، صنایع دفاعی، صنایع غذایی و ... بسیار حائز اهمیت است. با استفاده از تجهیزات ابزار دقیق، میتوان پارامترهایی مانند فشار، دما، سطح، حرکت، جریان، pH، اکسیژن، رطوبت، و... را با دقت و صحت بالا اندازهگیری کرد.
به طور کلی، استفاده از تجهیزات ابزار دقیق بهبود کیفیت و کارایی فرآیندهای صنعتی و همچنین کاهش هزینههای تولید و افزایش بهرهوری کمک میکند. همچنین، با استفاده از این تجهیزات میتوان خطاهای اندازهگیری و کنترلی را به حداقل رساند و عملیات تولید را بهبود بخشید. بنابراین، استفاده از تجهیزات ابزاردقیق در صنایع مختلف بسیار مهم است و به کیفیت و دقت بالاتر تولیدات کمک میکند.
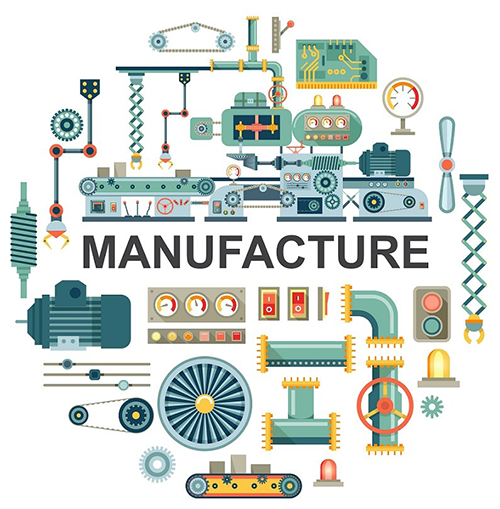
چگونه تجهیزات ابزار دقیق میتوانند به کاهش هزینههای تولید کمک کنند؟
استفاده از تجهیزات ابزار دقیق در فرآیندهای تولید، میتواند به کاهش هزینههای تولید کمک کند به دلایل زیر:
- کاهش خطاهای اندازهگیری: استفاده از تجهیزات ابزار دقیق با دقت بالا، میتواند به کاهش خطاهای اندازهگیری در فرآیندهای تولید کمک کند. این کاهش خطاها باعث میشود که محصولات با کیفیتتر و با مشخصات دقیق تر تولید شود و از این رو هزینههای ناشی از عیبهای محصولات کاهش پیدا کند.
- بهبود دقت کنترل پارامترها: استفاده از تجهیزات ابزار دقیق با دقت بالا، میتواند به بهبود دقت کنترل پارامترهای مختلف در فرآیندهای تولید کمک کند. این کنترل دقیق تر باعث میشود که عملیات تولید بهینهتر شود و به همین دلیل هزینههای تولید نیز کاهش پیدا میکند.
- بهبود کیفیت محصولات: استفاده از تجهیزات ابزار دقیق باعث بهبود کیفیت محصولات تولیدی میشود. این بهبود کیفیت میتواند به کاهش هزینههای مربوط به بازگشت محصولات و هزینههای تست و بازرسی کمک کند.
- بهبود بهرهوری: استفاده از تجهیزات ابزار دقیق با دقت بالا باعث بهبود بهرهوری در فرآیندهای تولید میشود. بهبود بهرهوری در این راستا به کاهش هزینههای تولید کمک میکند. به عنوان مثال، با داشتن دادههای دقیق و رصد دقیق فرآیندهای تولید، میتوان بهینهسازی فرآیندهای تولید را انجام داد و هزینههای تولید را کاهش داد.
- کاهش زمان تعمیر و نگهداری: استفاده از تجهیزات ابزار دقیق با دقت بالا، میتواند به کاهش زمان تعمیر و نگهداری این تجهیزات کمک کند. این کاهش زمان تعمیر و نگهداری باعث میشود که فرآیندهای تولید با کمترین توقف و تعطیلی انجام شود و هزینههای مربوط به توقف تولید کاهش پیدا کند.
- بهبود سرعت تولید: استفاده از تجهیزات ابزار دقیق با دقت بالا، میتواند به بهبود سرعت تولید در فرآیندهای تولید کمک کند. با داشتن دادههای دقیق و رصد دقیق فرآیندهای تولید، میتوان فرآیندهای تولید را بهینهسازی کرده و سرعت تولید را افزایش داد. این بهبود به سرعت تولید محصولات و در نتیجه کاهش هزینههای تولید کمک میکند.
بنابراین، استفاده از تجهیزات ابزار دقیق در فرآیندهای تولید، با بهبود دقت اندازهگیری و کنترل پارامترهای مختلف، بهبود کیفیت محصولات، بهبود بهرهوری، کاهش زمان تعمیر و نگهداری و بهبود سرعت تولید، میتواند به کاهش هزینههای تولید کمک کند. به طور کلی، استفاده از تجهیزات ابزار دقیق با دقت بالا در فرآیندهای تولید، میتواند به کاهش هزینههای تولید و افزایش بهرهوری و سودآوری کمک کند.
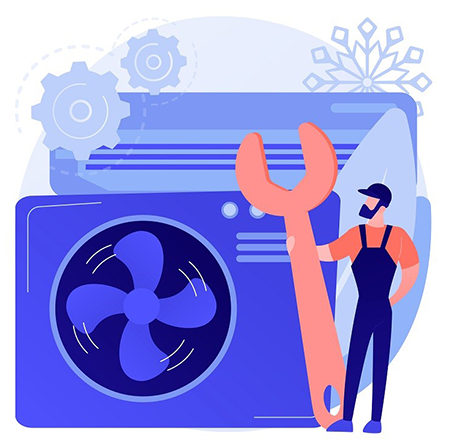
خرید ابزار دقیق
با توجه به تنوع محصولات در حوزه ی ابزار دقیق، در صورت ندانستن کد و مدل محصول، انتخاب و خرید ابزار دقیق برای شما سخت و گیج کننده خواهد بود. در این محتوا تلاش بر این است تا شما را با نکات مهم هنگام خرید ابزار دقیق مورد نیاز راهنمایی کنیم تا انتخابی درست داشته باشید. خرید ابزار دقیق برای کاربردهای مختلف، از جمله صنعت، پزشکی، تحقیقات علمی و غیره، بسیار مهم است. در ادامه به برخی از نکات مهم هنگام خرید ابزار دقیق اشاره میکنم:
- دقت در انتخاب نوع و مدل دستگاه: قبل از خرید، باید به دقت نوع و مدل دستگاه را با توجه به کاربرد مورد نظر انتخاب کرد. برای مثال، یک دستگاه دماسنج با دقت بالا برای پزشکی و یا محیط هایی که نیاز به دقت بالایی دارند، مناسب است. این دقت در پزشکی در حد صدم درجه ی سانتیگراد است در صورتی که در محیط های صنعتی دقت یک درجه تا دو درجه هم قابل قبول است.
- بررسی دقیق مشخصات فنی دستگاه: برای اطمینان از دقت و درستی دستگاه، باید مشخصات فنی آن را با دقت بررسی کنید. این موارد شامل دقت اندازه گیری، محدوده اندازه گیری، دمای کاری، رطوبت محیط، زمان پاسخگویی و دوره کالیبراسیون است.
- بررسی صلاحیت سازنده و محصول: برای اطمینان از کیفیت و قابلیت اطمینان دستگاه، باید سازنده و محصول را با دقت بررسی کنید. بهتر است از شرکتهای معتبر و معروف خرید کنید و نظرات کاربران دیگر را مطالعه کنید.
- بررسی قیمت و مقایسه با دیگر محصولات: قیمت دستگاه نیز یکی از مهمترین عوامل خرید است. برای اطمینان از اینکه قیمت دستگاه مناسب و عادلانه است، میتوانید با دیگر محصولات مشابه مقایسه کنید و قیمت را با دقت بررسی کنید.
- بررسی شرایط گارانتی و خدمات پس از فروش: برای اطمینان از اینکه در صورت وجود مشکل در دستگاه، شرایط گارانتی و خدمات پس از فروش مناسب و قابل قبول هستند، باید شرایط گارانتی و خدمات پس از فروش را با دقت بررسی کنید.
- انتخاب فروشنده معتبر: نهایتاً، برای اطمینان از کیفیت و اصالت دستگاه، باید از فروشنده معتبر و قابل استفاده کنید. فروشندگان معتبر معمولاً دستگاههایی را ارائه میدهند که از کیفیت بالایی برخوردارند و همچنین خدمات پس از فروشی را به مشتریان خود ارائه میدهند.
به طور کلی، خرید ابزار دقیق برای کاربردهای مختلف بسیار مهم است و باید با دقت بسیاری انجام شود. با توجه به موارد فوق و دیگر نکات مرتبط، میتوانید بهترین تجربه خرید را داشته باشید و از دستگاهی با کیفیت و صحیح برای کاربرد خود بهرهمند شوید.
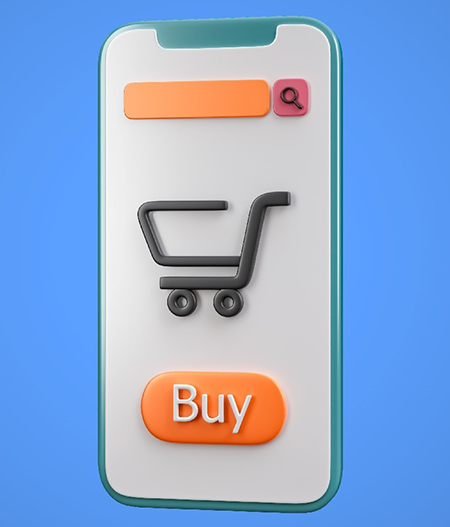
برندهای معتبر در خرید ابزار دقیق
برندهای مختلفی چه داخلی و چه خارجی در زمینه ی تولید و ساخت انواع ابزار دقیق فعالیت می کنند. البته باید به این نکته توجه داشت که شرکتهای معتبر و معروف در هر کشور و منطقه ممکن است متفاوت باشند، بنابراین در انتخاب شرکت، نیاز به بررسی موارد محلی دارید. در ادامه چند شرکت معتبر و جهانی را برای خرید ابزار دقیق معرفی میکنیم:
- امرسون (Emerson): شرکت آمریکایی امرسون یکی از بزرگترین شرکت های جهانی در زمینه تولید ابزار دقیق و سیستمهای کنترل است.
- سیمنز (Siemens): شرکت سیمنز یکی از بزرگترین شرکتهای جهانی در زمینه تولید ابزار دقیق، سیستمهای کنترل و اتوماسیون صنعتی است.
- هانیول (Honeywell): شرکت هانیول یکی از برترین شرکت های جهانی در زمینه تولید ابزار دقیق، سیستمهای کنترل و اتوماسیون است. یکی از برترین برند های آمریکایی است.
- یوکوگاوا (Yokogawa): شرکت ژاپنی یوکوگاوا یکی از بزرگترین شرکت های جهانی در زمینه تولید ابزار دقیق و سیستمهای کنترل است.
- اندرس هاوزر (Endress+Hauser): شرکت لول ترانسمیتر | اندرس| اندرس هاوزر یکی از برترین شرکت های جهانی در زمینه تولید ابزار دقیق و سیستمهای کنترل است. این شرکت بیشتر در زمینه تولید سنسورها و تجهیزات اندازهگیری فشار، دما، جریان و سطح فعالیت دارد.
- فلوک (Fluke): شرکت فلوک یکی از برترین شرکت های جهانی در زمینه تولید ابزار دقیق دستی و تجهیزات تست و اندازهگیری است. برند فلوک یک برند آمریکایی است.
- کیوریتسو (KYORITSU): شرکت ژاپنی کیورستو به عنوان یک شرکت تولید کننده انواع ابزارهای دقیق مانند میکرومتر، کالیبراتور، طبقهبندی و دستگاههای اندازهگیری فعالیت میکند و با داشتن تکنولوژی پیشرفته، به عنوان یکی از برترین شرکتهای جهانی در زمینه تولید ابزار دقیق شناخته میشود.
- فیشر (Fisher): شرکت فیشر به عنوان یک شرکت تولید کننده انواع سوئیچ و والوهای صنعتی و ابزارهای کنترلی، در زمینه تولید ابزار دقیق فعالیت میکند و یکی از بزرگترین شرکتهای جهانی در این زمینه است.
- اومرون (Omron): شرکت اومرون یکی از برترین شرکتهای جهانی در زمینه تولید ابزار دقیق و تجهیزات کنترل واتوماسیون صنعتی است و به طور خاص در زمینه تولید سنسورها و تجهیزات اندازهگیری فشار، دما، جریان و سطح فعالیت دارد.
- فیلیپس (Philips): شرکت فیلیپس به عنوان یکی از بزرگترین شرکتهای جهانی در زمینه تولید ابزار دقیق پزشکی، از جمله دستگاههای سنجش فشار خون، دستگاههای سنجش قند خون و دستگاههای اکسیمتر فعالیت میکند.
- آلن بردلی (Allen Bradley): شرکت آلن بردلی به عنوان یکی از برترین شرکتهای جهانی در زمینه تولید سیستمهای کنترل و اتوماسیون صنعتی و ابزار دقیق، فعالیت میکند. در زمینه تولید این شرکت، انواع سنسور فشار، سنسور دما، جریان،کالیبراتور جریان | ولتاژ| ولتاژ و سطح، کنترلرهای برنامهپذیر و دستگاههای اتوماسیون صنعتی میباشد.
- ویکا (WIKA): این شرکت یکی از معروفت ترین شرکت های تولید کننده در حوزه ی گیج فشار و گیج دما است. قطعا هنگام خرید سنسور | ترانسمیتر ph|سنسور ORP | ترانسمیتر phهای دما و فشار اسم این برند را خواهید شنید.
به طور کلی، شرکتهایی که در زمینه تولید ابزار دقیق فعالیت میکند، بسیار زیاد هستند و این فهرست تنها چند نمونه از آنهاست. برای انتخاب بهترین شرکت برای نیاز خود، باید به مشخصات و نیازهای خود توجه کنید و با مطالعه و بررسی دقیق، شرکت مناسب را برای خود پیدا کنید. همچنین، بهتر است قبل از خرید، نظرات و تجربیات کاربران دیگر را نیز مطالعه کنید.
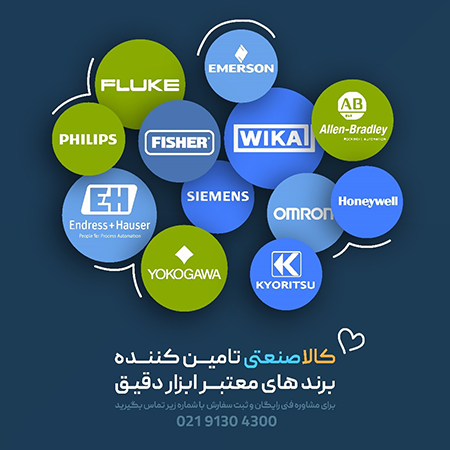
برند های داخلی جهت خرید ابزار دقیق
با توسعه صنعت در داخل کشور و اهمیت آن، شرکت های دانش بنیان فرصت مناسبی برای عرضه ی کالاهای با کیفیت و مناسب با شرایط بازار را پیدا کردند. با توجه به اینکه تهیه ی برندهای اروپایی گاها سخت و زمان بر است استفاده از برندهای ایرانی نه تنها فرصت خوب و مناسبی برای صنعتگران است بلکه برای شرکت های دانش بنیان نیز فرصت مناسبی است تا کالاهای با کیفیت و قیمت خوبی را به بازار ارائه دهند. در زیر برخی از این برندهای خوب ایرانی را معرفی می کنیم.
- پریسماتک: شرکت کنترل سیستم خاورمیانه با نام تجاری پریسماتک از سال 1387 توسط عده ای از نخبگان، محققان و متخصصان در زمینه ی اتوماسیون کار خود را آغاز کرد و در سال 1393 مفتخر به کسب عنوان دانش بنیان از سوی بنیاد ملی نخبگان شد.
- این شرکت در حال حاضر، در زمینه ی ساخت انواع فلومتر مغناطیسی، کوریولیس، رفرکتومتر و کانداکتیویتی متر فعالیت دارد. از مزایای دیگر استفاده از این برند، گارانتی محصولات و خدمات پس از فروش این برند است.
- آداک سنجش کویر: شرکت آداک سنجش از سال ۱۳۹۶ فعالیت خود را در زمینه طراحی و ساخت تجهیزات ابزار دقیق با هدف ساخت و تولید محصولات با کیفیت آغاز کرد. این شرکت با شناخت نیازهای صنعت و صنعتگران, سعی بر آغاز و گسترش تجهیزات اندازه گیری و عرضه آن در بازار ایران نمود و با اتکا به تجارب غنی و با ارزش حاصله از انجام پروژه های بزرگ ابزار دقیق، در حال حاضر پیشرفت شایانی در ساخت و به روزرسانی، محصولات هم سطح با تکنولوژی روز دنیا را دارد. همچنین این شرکت درسال ۱۳۹۷ موفق به کسب عنوان دانش بنیان از سوی معاونت علمی ریاست جمهوری گردیده است. لازم به ذکر است در حال این شرکت در زمینه ی تولید لول سوئیچ خازنی و لول سوئیچ پره ای و همچنین لولسنسور ORP | ترانسمیتر | نمایشگر صنعتیهای خازنی فعالیت دارد.
- آکام مدار آسان: این شرکت دانش بنیان در سال 1397 به عنوان اولین تولید کننده ی فلومتر های هوشمندسنسورسنسور القایی | مجاورتی |سنسور مجاورتی | التراسونیک فعالیت خود را زیر نظر متخصصین و محققان برتر کشور آغاز کرد. شرکت آکام مدار آسان با هدف ارائه راهکارهای اندازه گیری نو آورانه برای مصرف انرژی پا به این عرصه گذاشته است.
شرکت های دانش بنیان گوناگونی در حال حاضر آماده ارائه خدمات به مشتریان در حوزه ی خرید ابزار دقیق هستند که توانایی های شایانی در این عرصه دارند. لازم به ذکر است با توجه به شرایط بازار و ارائه خدمات خوب و شایسته ی برندهای داخلی، از آنها در انواع پروژه های خود استفاده کنید.
معرفی پارامترهای مهم و بررسی شرکت ها در زمینه فروش ابزار دقیق
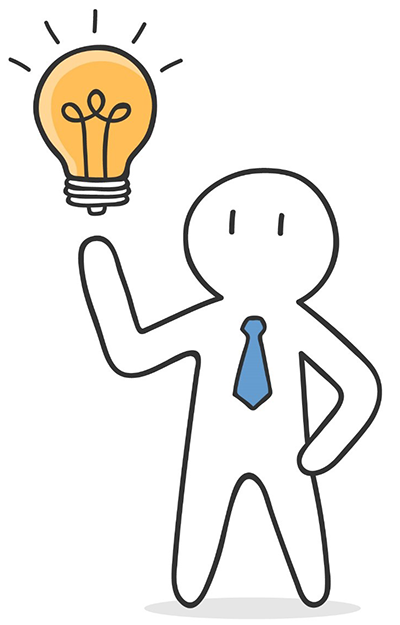
در انتخاب بهترین شرکت برای خرید ابزار دقیق، میتوانید به نکات زیر توجه کنید:
- کیفیت محصولات: در انتخاب شرکت، باید به کیفیت محصولات اهمیت بدهید. باید به دنبال شرکتی باشید که محصولات با کیفیت و مطابق با استانداردهای جهانی تولید کند.
- تنوع محصولات: اگر شما نیاز به چندین نوع محصول دارید، بهتر است شرکتی را انتخاب کنید که تنوع محصولات زیادی دارد.
- قیمت: مهمترین عامل در انتخاب شرکت، قیمت محصولات است. باید به دنبال شرکتی باشید که محصولات خود را با قیمت مناسب ارائه می دهد در نظر داشته باشید قیمت را با کیفیت محصولات مقایسه کنید.
- خدمات پس از فروش: برای اطمینان از خرید درست، بهتر است به خدمات پس از فروش شرکت توجه کنید. شرکتی که خدمات پس از فروش خوبی داشته باشد، به شما در صورت بروز مشکلات در آینده کمک خواهد کرد.
- تجربه شرکت: تجربه شرکت در زمینه تولید محصولات مورد نیاز شما، نیز مهم است. شرکتی با تجربه بیشتر، میتواند بهترین محصولات را با کیفیت بالا تولید کند و به شما در رفع مشکلات کمک کند. همچنین در صورت نیاز می توانید هنگام خرید از تجربه ی آنها در زمینه ی خرید دستگاه مورد نیاز خود کمک بگیرید.
- رضایت مشتریان: نظرات و تجربیات مشتریانی که با شرکت قبلی همکاری کردهاند، میتواند به شما در انتخاب شرکت مناسب کمک کند. بررسی نظرات و تجربیات مشتریان در مورد شرکت، میتواند به شما در انتخاب بهتر کمک کند.
- حمایت از محصولات داخلی: اگر با تولیدکنندگان داخلی همکاری کنید، میتوانید به اقتصاد کشور خود کمک کنید و به علاوه، بهترین محصولات را با قیمت مناسبتر بخرید.
- قابلیت ارائه خدمات شخصیسازی: برخی شرکتها میتوانند محصولاتشان را برای شما شخصیسازی کنند و به نیازهای شما بیشتر پاسخ دهند. اگر به محصولاتی با ویژگیهای خاص نیاز دارید، بهتر است شرکتی را انتخاب کنید که قابلیت ارائه خدمات شخصیسازی را داشته باشد.
- مدت زمان تحویل: در انتخاب شرکت، مدت زمان تحویل محصولات نیز بسیار مهم است. باید به دنبال شرکتی باشید که محصولات را در زمان مناسب و به موقع تحویل دهد.
- پشتیبانی فنی: شرکتی که پشتیبانی فنی قوی داشته باشد، میتواند به شما در رفع مشکلات فنی بعد از خرید محصول کمک کند. بنابراین، بهتر است شرکتی را انتخاب کنید که پشتیبانی فنی خوبی داشته باشد تا در صورت بروز هرگونه مشکل، به شما کمک کند و مشکلات را به سرعت حل کند.
کلام آخر
همان طور که پیداست ابزار دقیق در صنعت و سیستم های کنترلی نقش پر رنگی دارد و از اهمیت ویژه ای بر خوردار است از این رو خرید و فروش ابزار دقیق یکی از پر چالش ترین کارها در صنعت است، بررسی کالا ها از نظر پارامترهای مهم همچون دقت، تکرار پذیری و عدم موجودی کالاها از جمله مهمترین این چالش هاست، به همین علت پیشنهاد می شود در زمینه خرید ابزار دقیق با کارشناسان فنی در این زمینه مشورت کنید. کالاصنعتی به عنوان یکی از بزرگترین شرکت های خرید و فروش ابزار دقیق می تواند به شما در این زمینه راهنمایی و مشاوره های لازم را ارائه دهد. در این خصوص می توانید با کارشناسان فنی واحد ابزار دقیق شرکت کالاصنعتی در ارتباط باشید.